
Choose a piece wood and begin carving the face. Using a step-by-step video, follow along as the expert guides you through the process. The progressing cut will make carving the face much more realistic. It is important to create a lifelike facial expression by adjusting the position of the noses in the wood. In addition to the face outline, you may also choose colored dyes and shellac to add a realistic finish.
Hardwoods
When carving a face in wood, you must first consider the type of wood to be used. Hardwoods are a class of trees with broad leaves that grow in a variety of climate zones. Because of their wide range of density, strength, and appearance, hardwoods are suited for various purposes, including building and furniture. While hardwoods may be more affordable than softwoods due to their durability and fire resistance, they are still very durable.
If you are new to wood carving you might consider softwood such as butternut and basswood. These types of wood are easier to work with and are a good choice for beginners. You should keep in mind that soft woods will not have the same quality or finish as hardwoods. It is important to try different wood types before you settle on one.
Softwoods
The first step when carving a face in wood is choosing the softwood to use. Softwoods can be more difficult to carve because they often have more knots. They can also be more fragile if you use long strokes. Beginners will often cut small pieces of wood to reduce detail. This is not a big problem, but it is something to be aware.
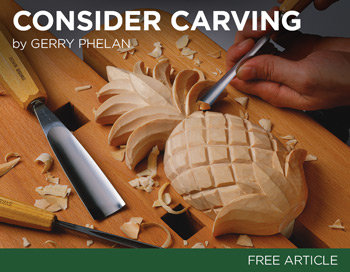
Some hardwoods are more difficult to work with than others. Aspen, butternut and basswood are some of the most easy to work with. A steeper bevel is better for this reason. Softwoods are also easier to work with than hardwoods, so you can carve them either along or across the grain. The quality of your finished product will depend on the wood you choose for carving.
Colored Dyes
Colored dyes can be used to give wood carvings a vivid, detailed look. These dyes can be purchased in many different colors. To create a unique color, you can add water or alcohol. You can mix colored dyes with shellac to make lighter woods. Use denatured alcohol to clean your brushes after you have applied the dyes. Another option is paste wax. Be aware that an excessive glossiness may distract from your work. Use 0000 Steel Wool to remove any excessive glossiness.
There are many types of wood dyes that can be used and they are easy to apply. Wood dyes are compatible with all topcoats and are easy to apply. They also solve common finishing problems. They are easy to mix and use because they come in many primary colors. You can also mix and match them to your liking. They can even be blended to create unique colors.
Shellac
You should always have a jar of shellac handy before applying it to wood carvings. You can purchase a jar of shellac, but the easiest way to apply it is to use a brush. Two-pound cuts will suffice. This is because the shellac will gradually build up and will reduce brush marks. A thicker cut is better than a thin one because shellac can be very water-thin. Make your own pad out of small pieces of cotton and lintfree cloth. This will ensure you get the right amount. After that, dip the tip end of your brush in the shellac.
Shellac can be used for accenting grain or adding color. Shellac is available as a variety colors. This allows you to mix and match different shades of resin to create your own blends. The lac can be used to darken the color. Unlike some other wood finishes, shellac won't yellow or become cloudy over time. It will also last longer, so you can make more faces. You can also do this with any wood carving project.
Gouges
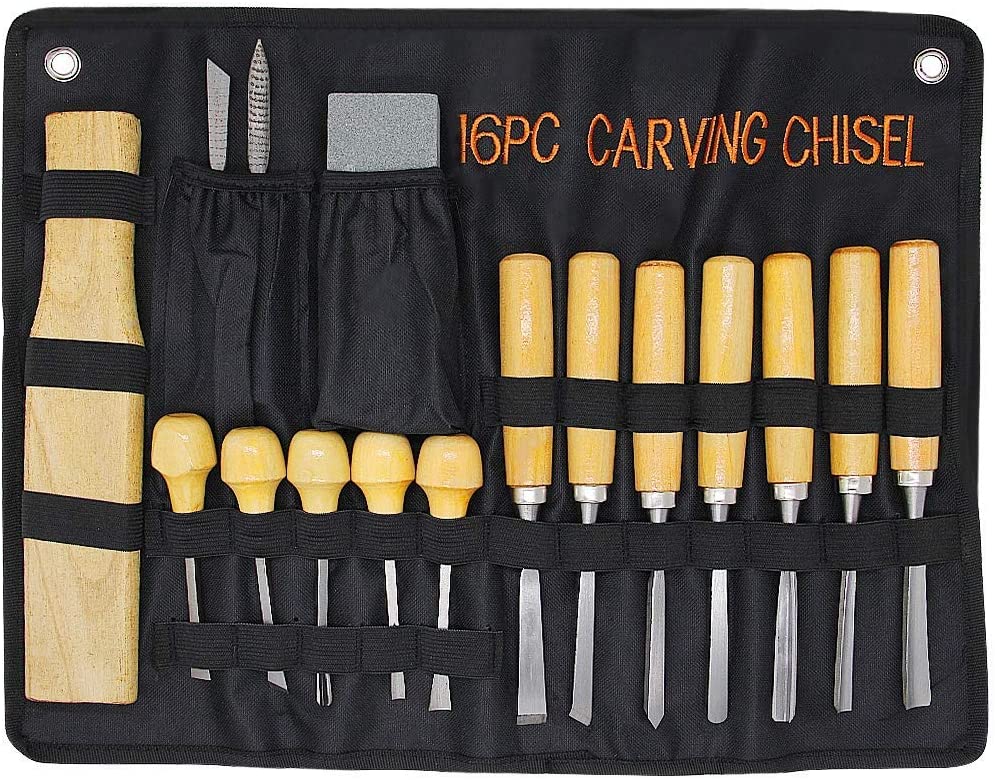
There are many sizes and shapes of gouges. The straight and the palm gouges types are the most commonly used. Palm gouges can be held in one hand, while straight gouges require a larger handle and shaft. Hand held carving becomes much easier when the handles are shorter. Also known as veiners, palm gouges are great for carving faces in wood. Here are some tips before you start carving.
First, learn how to choose the best gouge. You need a gouge that can carve a shallow groove. A sharp edge and small sweep are essential features of a good gouge. Gouges are commonly classified by size. A 3/10 size gouge can make the same cut as a 5-/10 size gouge. As the first number increases the scoop between edges becomes deeper, and the sweep becomes progressively curvier. A gouge with a small sweep will be able to carve a shallow v-shaped profile.
FAQ
What is the difference between a hobbyist or a professional woodworker, and how can you tell?
Hobbyists like making things with wood. Professionals focus more on quality. Hobbyists take great pride in their creations, and share them with family and friends. Before they start working on a project, professionals will spend hours researching the designs. They'll be meticulous about every aspect of their work, from choosing the best materials to finishing it perfectly.
What kind of wood should you use?
The most commonly used woods for woodworking are oak, maple, cherry. Each wood variety has distinct characteristics that influence the final product's look and feel. Oak, for example, tends be darker and more hard than other woods. Birch is soft and light, and mahogany is denseer and heavier. There are two options: solid wood and veneers. Veneers consist of thin sheets made from wood and glued together to form a single layer.
What would be your first step in woodworking?
Start off with softwood like pine and poplar. When you feel confident with these two, move on towards hardwood.
What are the basics of woodworking?
A great way to start learning how to build furniture is by building a simple bench for yourself. You can use any wood you have in your home to complete this project. If you aren't sure what type of wood to use, you can buy cheap pine boards from Lowes or Home Depot. You'll need to sand the bench after it's built. Then, finish it with varnish or a stain.
How often should new supplies be purchased?
Some tools will need to be replaced over time. Sharpening hand tools is a must. If you are using power tools, you will need to purchase replacement parts regularly. Spread your purchases over several months to avoid purchasing too many items at once.
Statistics
- If your lumber isn't as dry as you would like when you purchase it (over 22% in Glen Huey's opinion…probably over 10-15% in my opinion), then it's a good idea to let it acclimate to your workshop for a couple of weeks. (woodandshop.com)
- The best-paid 10 percent make $76,000, while the lowest-paid 10 percent make $34,000. (zippia.com)
- Average lumber prices rose about 600 percent between April 2020 and May 2021. (familyhandyman.com)
- Woodworkers on the lower end of that spectrum, the bottom 10% to be exact, make roughly $24,000 a year, while the top 10% makes $108,000. (zippia.com)
External Links
How To
How to stain wood
Stain wood is a process that involves applying chemicals to the surface of wood, which changes its color. This chemical reaction changes the wood's color from white to brownish. Oak is the most common wood type for staining. However, you can also use other wood types.
There are many ways to stain wood surfaces. Some methods involve mixing the stain with a solvent (such as turpentine) and then brushing or spraying the mixture onto the wood. Others use a solution made up of water and dye, which is then applied directly onto the wood. The stain can be mixed with paints and varnishes to become part of the final coating.
Preparing your wood for staining is the first thing to do. To apply the stain, clean the wood completely. Sanding the wood removes scratches and imperfections. The next step is to choose the stain type you want. Penetrating stains are different from non-penetrating. Penetrating colors penetrate deeper into wood than those that are non-penetrating. This makes them more suitable for darker colors, such as mahogany. Non-penetrating stains work best with light colors like maple.
You will need to decide on the type of stain you want to use, and then prepare your tools. Because you can spread the stain evenly with a paintbrush, it is ideal for applying them. After you're done painting, make sure to have some rags handy to remove any excess stain. If you plan to mix the stain yourself, make sure you have enough containers available to hold the different components of the mixture.
Once you have prepared your materials, start by cleaning the area where you plan to stain the wood. You can remove grime and dirt with warm water and soap. You can wipe down the entire furniture using a damp rag with clean water. Make sure you eliminate any loose debris, especially if you plan to stain darker wood.
Apply the stain. The stain can be applied by spraying or brushing the stain onto one end of the furniture. Move slowly and carefully along the grain of your wood until you reach its opposite end. The stain should not drip off of the wood's edge. Before you proceed with the next steps, let the stain dry completely.
A coat of clear polyurethane sealing agent is applied to protect the paint. Three coats are recommended for polyurethane. Allow the third coat, which should dry overnight, to dry before sanding.