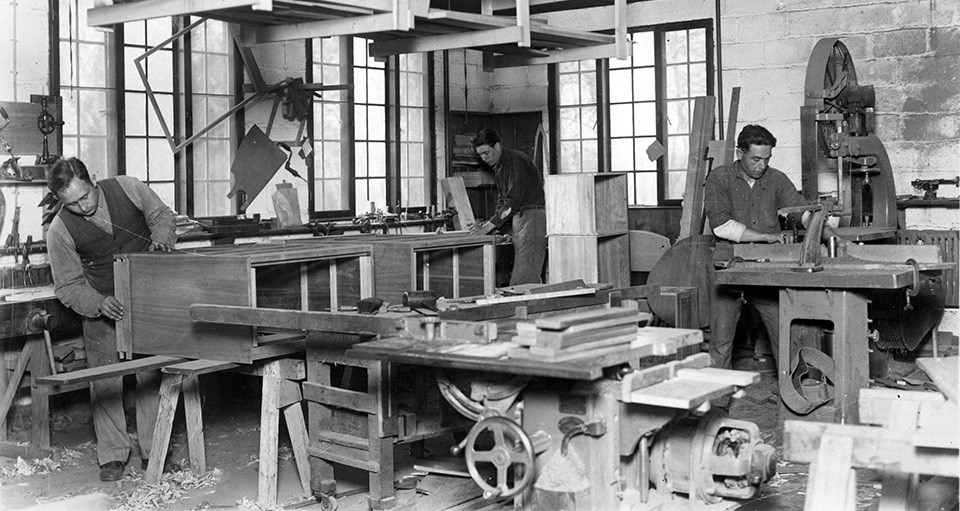
Philip Moulthrop began turning wooden in 1979. He learned his craft from his dad, Ed Moulthrop. He cuts the green parts of trees in the southeastern region using a chain saw and a hand-forged lathe. He then refines the bowl on the lathe, finishing it with several coats of finish. The whole process can take between four months and a year. Once complete, the bowls are ready to be purchased or given as gifts.
Philip Moulthrop
The Phillip Moulthrop bowl is a stunning red leopard maple vessel. He developed the wood turning process, which has been a family heritage for three generations. In addition to their own creations, Philip Moulthrop's bowls are part of the permanent collections of several prominent museums and private collections around the world. Here are some of their most renowned pieces. For more information about this talented artist, read on.
The American artist Philip Moulthrop was born in 1947. In his 20s, he studied general arts and soon discovered a passion for woodworking. At age 16, he bought his first lathe and gradually expanded his equipment. He created beautiful, turned vessels which attracted the attention and support of the arts community as well as the president of the United States. After his work was acknowledged, he began to sell his pieces at local craft fairs. His work began to be recognized internationally.
Matt Moulthrop
The Matt Moulthrop-Bowls are a stunning example of Georgia’s rich wood turning tradition. The artist was born in Atlanta and received his BA and MBA from Georgia Tech. Although he spent a couple of years in the world of 9-to-5 jobs, he never forgot his passion for turning wood. He won national recognition for his bowls. His works can be seen at the ASU Art Museum and Carter Center, as well as the Racine Art Museum.
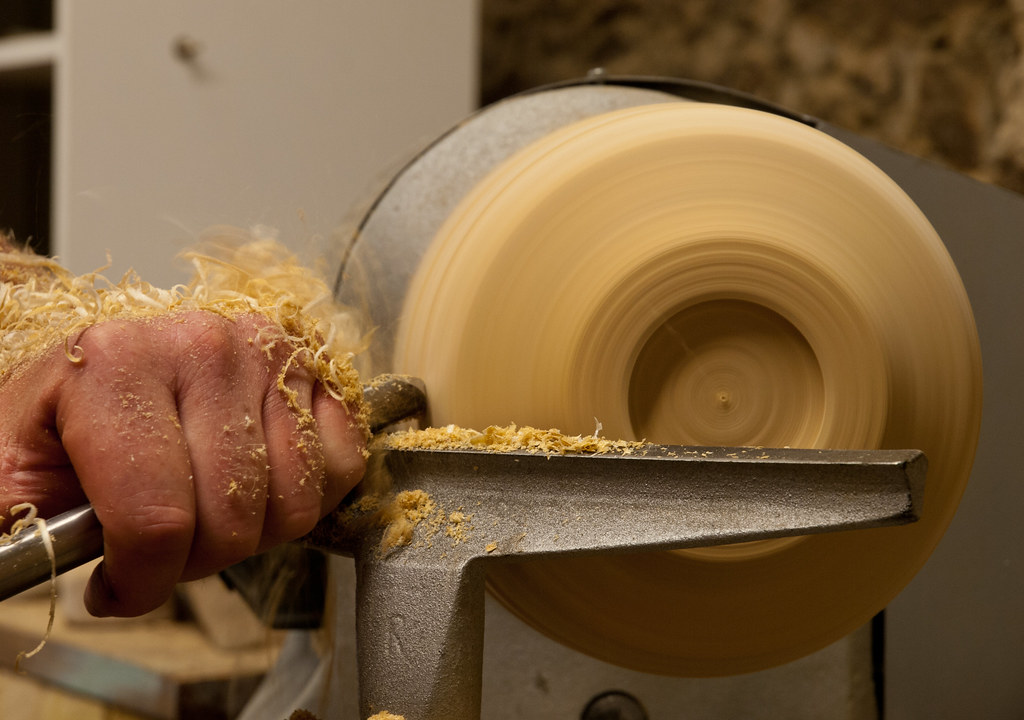
The Moulthrops are world-class wood-turners and have had works in major collections both in the United States of America and internationally. Moulthrop's own pieces are held in the Renwick Gallery of the National Museum of American Art. Collectors from all over the globe have taken to heart his bowls. During a Smithsonian photo shoot, the bowl maker gave each photographer a signed copy.
Ed Moulthrop
Moulthrop began turning bowls in the early 1970s and soon earned a scholarship to Princeton University to study architecture. Moulthrop spent a year in Vietnam and then resigned as an architect to pursue woodturning. His large-scale, turned bowls are internationally recognized and can be found in museums like the Museum of Arts and Design in New York and the White House Collection of American Crafts. These bowls have a clear, polished finish and are made of domestic woods.
The Ed Moulthrop rare bowl measures nine by fourteen inches in size and is made from wild cherries. These wood bowls can be purchased at Gump's in San Francisco. Many other Ed Moulthrop wood bowls are on display. The best way to learn about the artist's work is to visit the exhibition. A beautiful catalogue of his work is also available. You can buy his bowls in museums but it is better to go to his studio and actually see it.
The Eagle & Phenix Dam Series
This limited edition collection of moulthrop bows uses wood from Eagle & Phenix Dam. The dam was built in Columbus, Georgia. These bowls are handcrafted by Phillip Moulthrop and Matt Moulthrop and have traces of their history. They can be bid upon during museum hours and some of them will be sold live.
The Moulthrop family has contributed to the growth of wood-turned bowls in Georgia. Three generations of the Moulthrop family have been turning bowls for over five decades, and the museum is proud to feature works from all of them. Many of these pieces are extremely prized because they have large sizes and smooth polished surfaces. His mosaic bowl technique, which involves glueing thin branches to a shaped bowl with thin branches, is featured in the exhibit.
Matt Moulthrop’s work
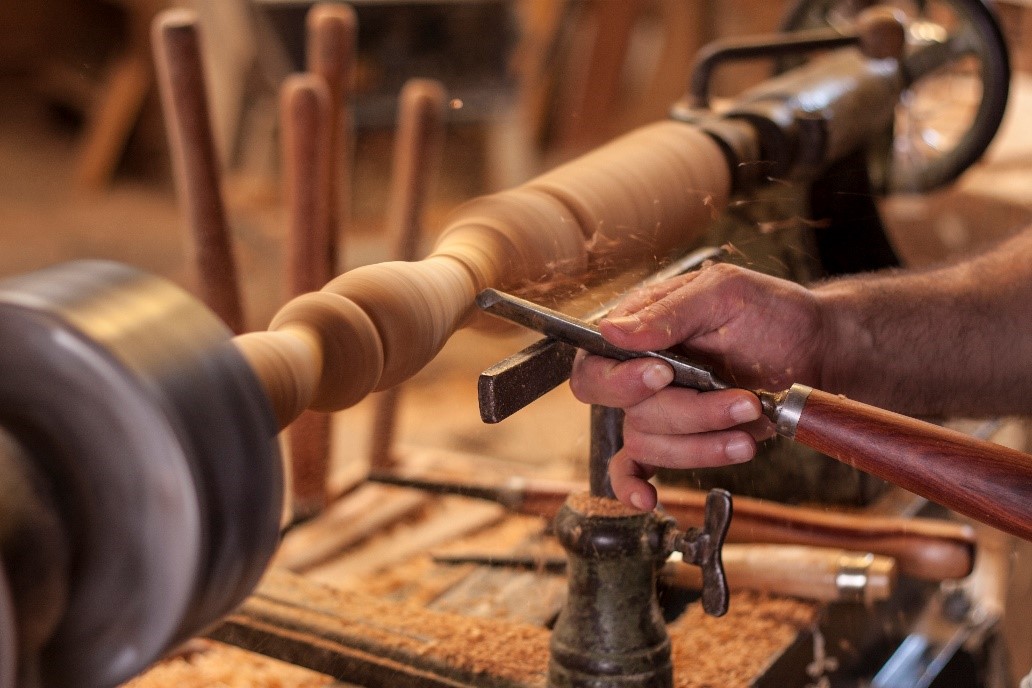
Matt Moulthrop was the son of Philip Moulthrop. At a young time, Matt was taught woodturning by his father. His passion for the craft grew from that point. Matt earned his BA at Georgia Tech and his MBA from Georgia Tech. After that, he turned his attention to woodworking as a profession. He is the third generation of woodworkers. His work is displayed in many prominent art institutions such as the ASU Art Museum, Carter Center and the Carter Center. He is currently working with commemorative pieces to mark the 100th anniversary for Georgia Tech Alumni Association.
He does not turn wood from Georgia. He also travels to other countries to search for unusual wood. He works with tools and a hand-forged turning lathe to make unique pieces from trees from all around the world. Wood from exotic places, such as volcanoes or underwater forests, is used to make his pieces. If you love his work, make sure you check it out!
FAQ
What is the difference between plywood and particle board?
Plywood can be described as a mixture of layers and wood that have been pressed together with pressure. Plywood can come in many thicknesses and is used for flooring and cabinets. Particle board is made up of sawdust mixed in resin, then compressed into large pieces. This board is commonly used in home improvement projects. Both boards are strong and can be easily cut.
Where do I get my woodworking supplies?
There are many places that you can find all the information you need. For example, you could visit local hardware stores or look online at websites like Amazon.com.
You might also consider flea markets and garage sale for any old furniture or other materials you could reuse.
What wooden items sell well?
Most wooden items that are best-sellers are made from wood harvested sustainably.
Maple, cherry, mahogany walnut, teak, mahogany and maple are the most common woods for furniture.
These woods are very strong, but they also have beautiful grain patterns and colors. If they are well cared for, they can last many years.
To protect wooden furniture from moisture damage, you should paint it first. This covers all surfaces, drawers included, as well as doors and handles.
If you want to make sure that your furniture lasts as long as possible, then you should choose a paint that is resistant to water.
A high-quality oil-based primer should be used, followed by two coats with top coat. Depending on how often it will be worn, you may need to apply several coats.
Spray cans and aerosol spray paints are not recommended. These products contain solvents that evaporate quickly and leave behind harmful fumes.
Statistics
- The best-paid 10 percent make $76,000, while the lowest-paid 10 percent make $34,000. (zippia.com)
- Overall employment of woodworkers is projected to grow 8 percent from 2020 to 2030, about as fast as the average for all occupations. (bls.gov)
- In 2014, there were just over 237,000 jobs for all woodworkers, with other wood product manufacturing employing 23 percent; wood kitchen cabinets and countertop manufacturing employing 21 percent. (theartcareerproject.com)
- The U.S. Bureau of Labor Statistics (BLS) estimates that the number of jobs for woodworkers will decline by 4% between 2019 and 2029. (indeed.com)
External Links
How To
How to make wood joint
This tutorial will demonstrate how to join two pieces together of wood. The "pocket hole joint" is a method whereby we drill holes into the wood and glue them together. This method is great if your wood's straight and smooth. If your wood isn't straight or flat, you might want to try another method, such as dowel joinery. Here are the steps
-
Drill Pocket Hole Joints. To start, measure and mark where you want to put the pocket hole joint. Use a jigsaw or handheld drilling machine to drill 3/8 inch deep holes at the ends of each wood piece.
-
Sand Smooth. Sanding the edges of the wood will help to prevent the joint from splitting later.
-
Glue Together Apply glue to both the ends of the wood. Allow it to sit for approximately 5 minutes before you clamp the pieces together.
-
Attach the Pieces together. After the glue has dried properly, clamp the pieces together to make sure they are flush.
-
Trim Joinery. After the glue dries completely, trim off any excess wood around the joint.
Be sure to leave enough space between each piece so that they can be turned inside-out.